Revitalizing Process Equipment with Re-glass Services

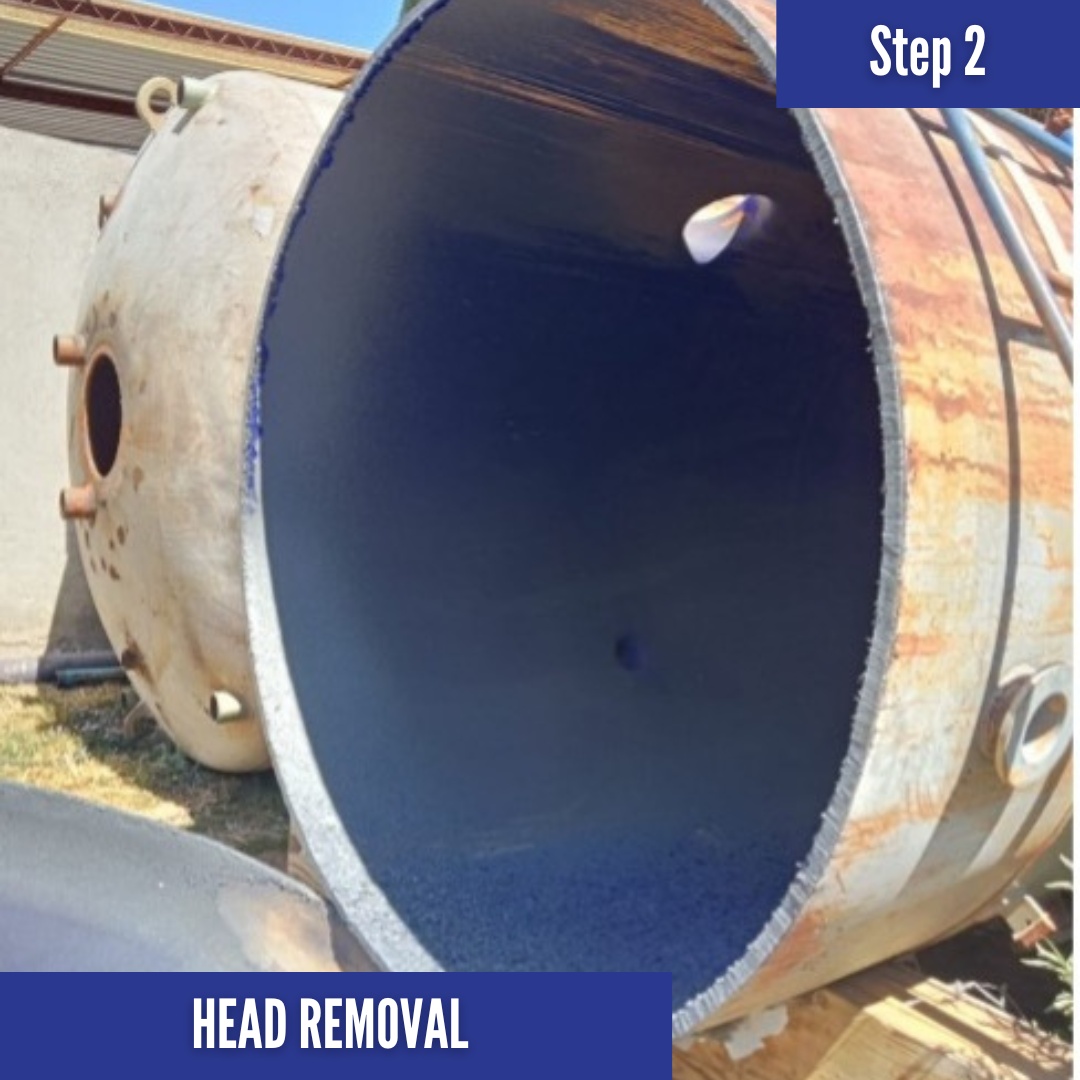



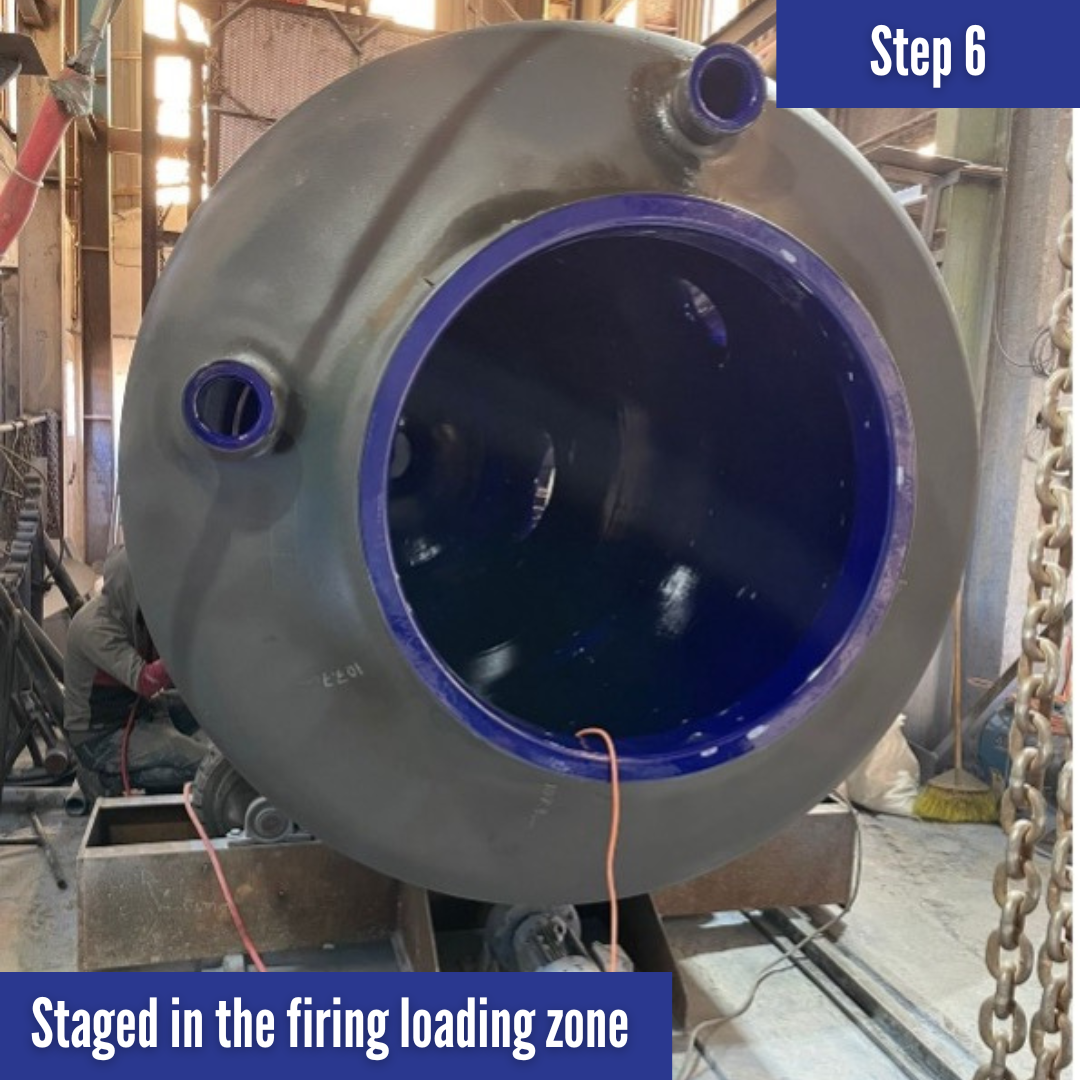

Glass lined process equipment, vital to many industrial operations, undergoes wear and tear over time. Erosion, thermal shock, and mechanical damage can reduce the glass thickness to below the acceptable 30 mils threshold, necessitating removal from service. Given the significant investment in such equipment, coupled with the high costs and long lead times associated with fabricating new vessels, reglassing presents a cost-effective, efficient alternative.
The GTI Reglassing/Rebuilt Advantage
Reglassing is a streamlined process that restores various components, such as access covers, agitators, baffles, valves, and reactors, to like-new condition. The benefits of reglassing include:
Cost Savings: Reglassing offers cost savings of 50% or more.
Warranty: Reglassed/Rebuilt equipment includes a 12-month warranty.
Service: GTI offers Field service technicians and engineers to support our equipment.
Time Efficiency: While new vitreous enamel equipment fabrication delivery is 7-9 months, reglassing can be completed in approximately ten-twelve weeks.
Quality Control: Each Vessel ships with a detailed inspection report with 20kv Spark test results, Statistical glass thickness analysis, ASME code calculations, Welder certifications, and AI review/authorization documents.
Certifications: ASME, ASTM, National Board.
Extend Equipment Life: The reconditioning process revitalizes existing equipment, extending its operational life and maintaining its performance standards. Glasslined Technologies can reglass and maintain ASME code status on Pfaulder, De Dieterich, 3V and ThaleTec. Our process meets ASTM B08.12 and EU standards for vitreous enamel.
The Reglassing Process
Evaluation and Preparation - The journey begins with a thorough evaluation of the vessel to determine its overall condition prior to shipment either with an onsite visit or detailed pictures to provide a cost estimate. This includes:
Initial Assessment: Before shipping, an initial assessment ensures the vessel meets basic reglassing criteria.
Decontamination of the equipment prior to loading.
Blocking/cribbing instructions.
GTI can arrange freight and loading
Upon arrival each item undergoes a detailed Inspection: including steel thickness measurements to identify areas needing ASME code repairs. Any required modifications, such as stud hole repairs or nozzle replacements, are noted in the work order.
Case Study: 14,000-Liter Vessel Regeneration
A 14,000-liter vessel, heavily damaged in operation, required urgent attention. The delivery time for a new vessel exceeded six months, making reglassing the optimal solution with a ten-week turnaround.
Head Replacement - The vessel's top head was damaged beyond repair, necessitating a complete replacement:
Pre-Order of new replacement ASME verified dished only Head and flanges: A new head was ordered prior to the vessel's arrival.
Removal of Damaged Head: The old, damaged head was carefully removed.
Installation of New Head: The new head, along with new nozzles in the same configuration, was installed. The jacket diaphragm was either replaced or repaired, and closure rings were added where necessary.
Stress Relief Treatment: The vessel underwent heat treatment to relieve stress before reglassing commenced.
Surface Preparation - Surface preparation is crucial for successful enameling:
Blasting: The vessel is blasted with special media to achieve the desired mil profile.
Cleaning: All dust and debris are meticulously removed to prevent contamination during the enameling process.
Enameling Process - The enameling process involves multiple stages to ensure optimal glass thickness:
Ground Coat Application: Applied in two firings, the ground coat forms the foundation layer.
Cover Coat Application: Up to nine firings build the glass thickness to the required level. Each layer's thickness is carefully monitored, and inspections are conducted after each firing to detect and address imperfections.
Quality Control and Finalization - Quality control is integral throughout the reglassing process:
QC Inspections: Detailed inspections after each firing ensure the glass integrity and thickness.
Documentation: A comprehensive dossier is compiled, including ASME code calculations, statistical glass thickness analysis, pressure tests, and flange alignment.
Epoxy Coating: Before shipment, the vessel is coated with a two-part epoxy coating for protection.
Crating for Shipment: The vessel is securely cribbed for safe transportation.
Re-glassing is a practical, efficient solution for maintaining and extending the life of glass lined process equipment. It offers significant cost savings, reduced downtime, and meticulous quality assurance, ensuring that equipment performs reliably long after its initial service life. By opting for re-glassing, companies can sustainably manage their process equipment assets, minimizing operational disruptions and maximizing investment returns.
We offer facilities in Mexico and USA.