Reactor 143 Repair: A Step-by-Step Overview

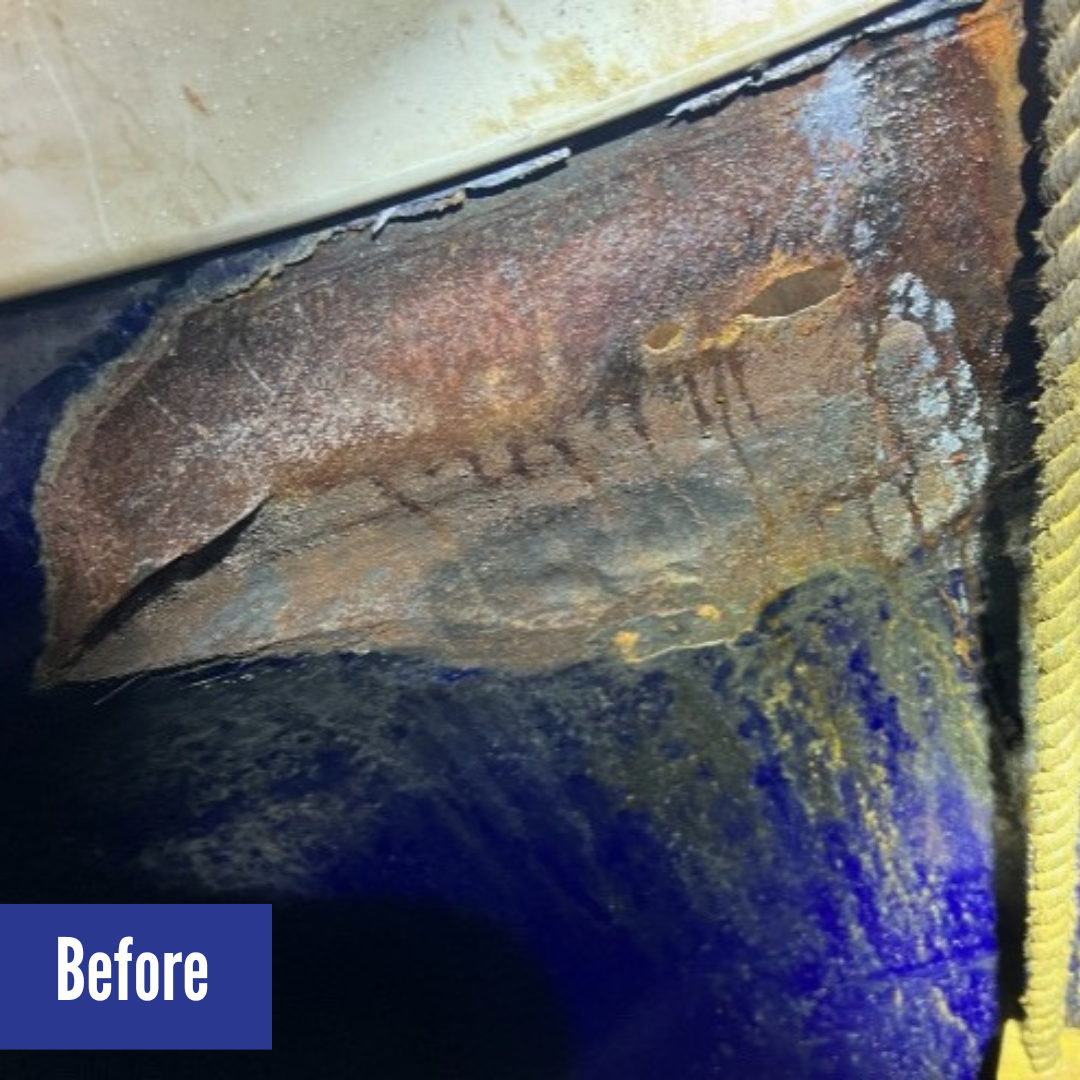
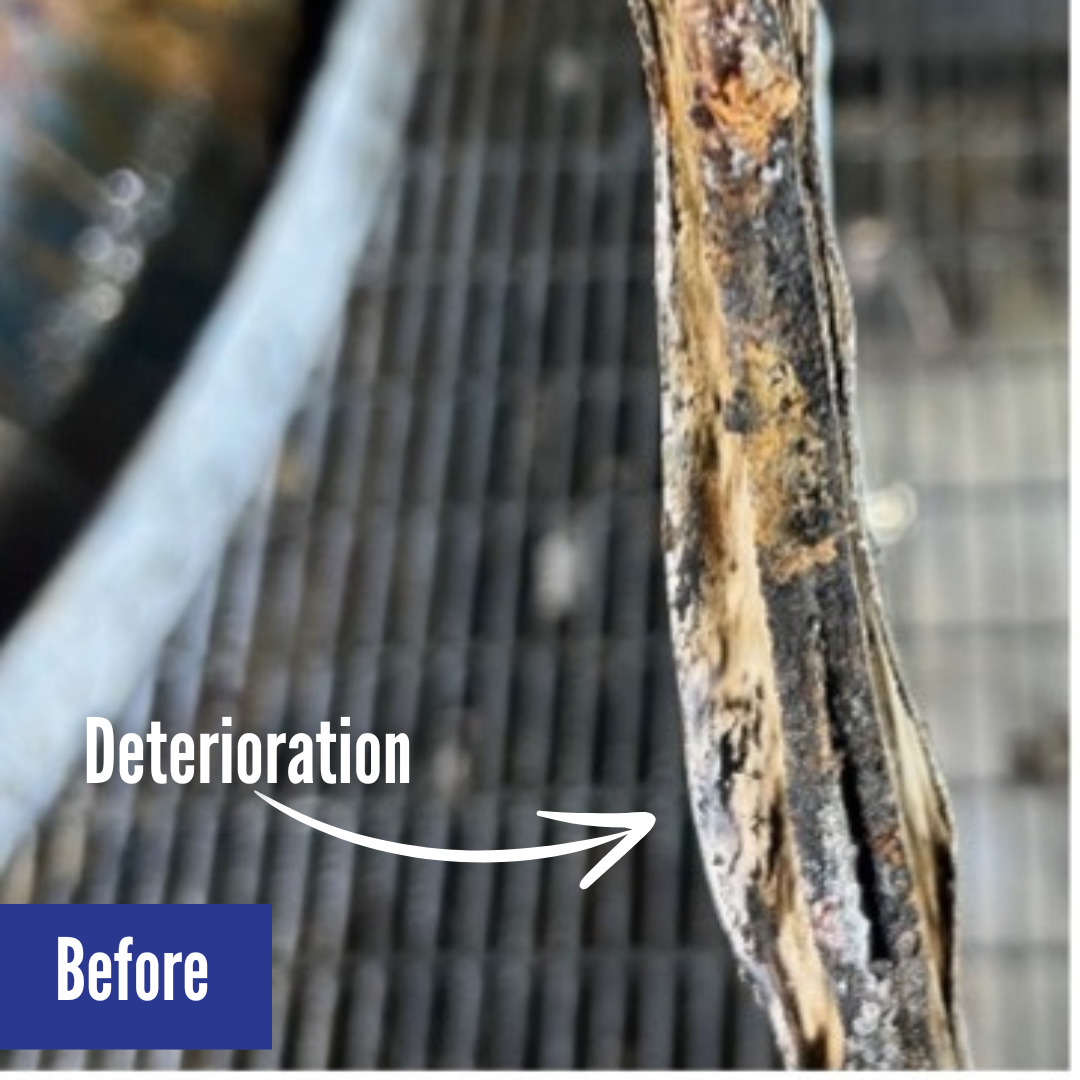
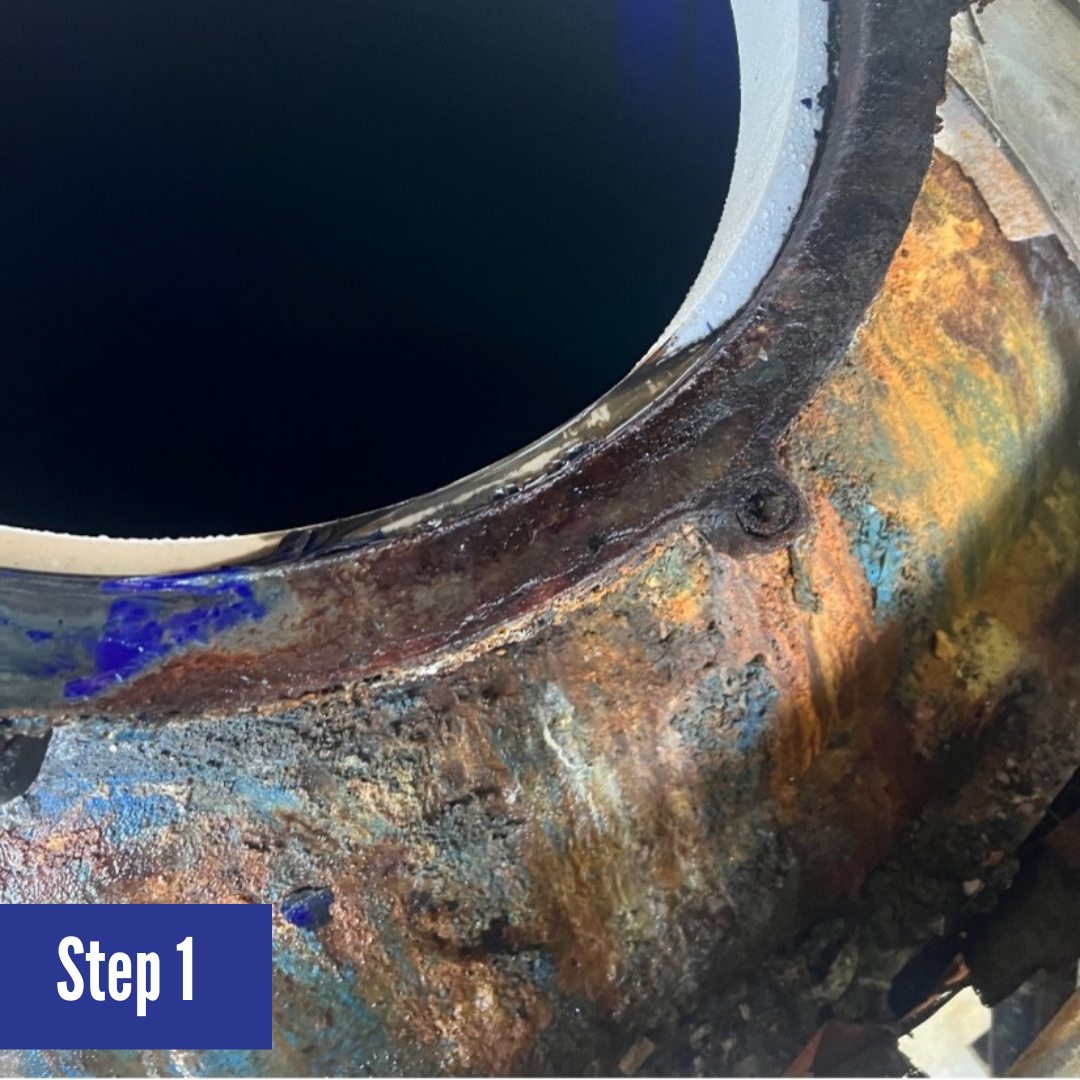
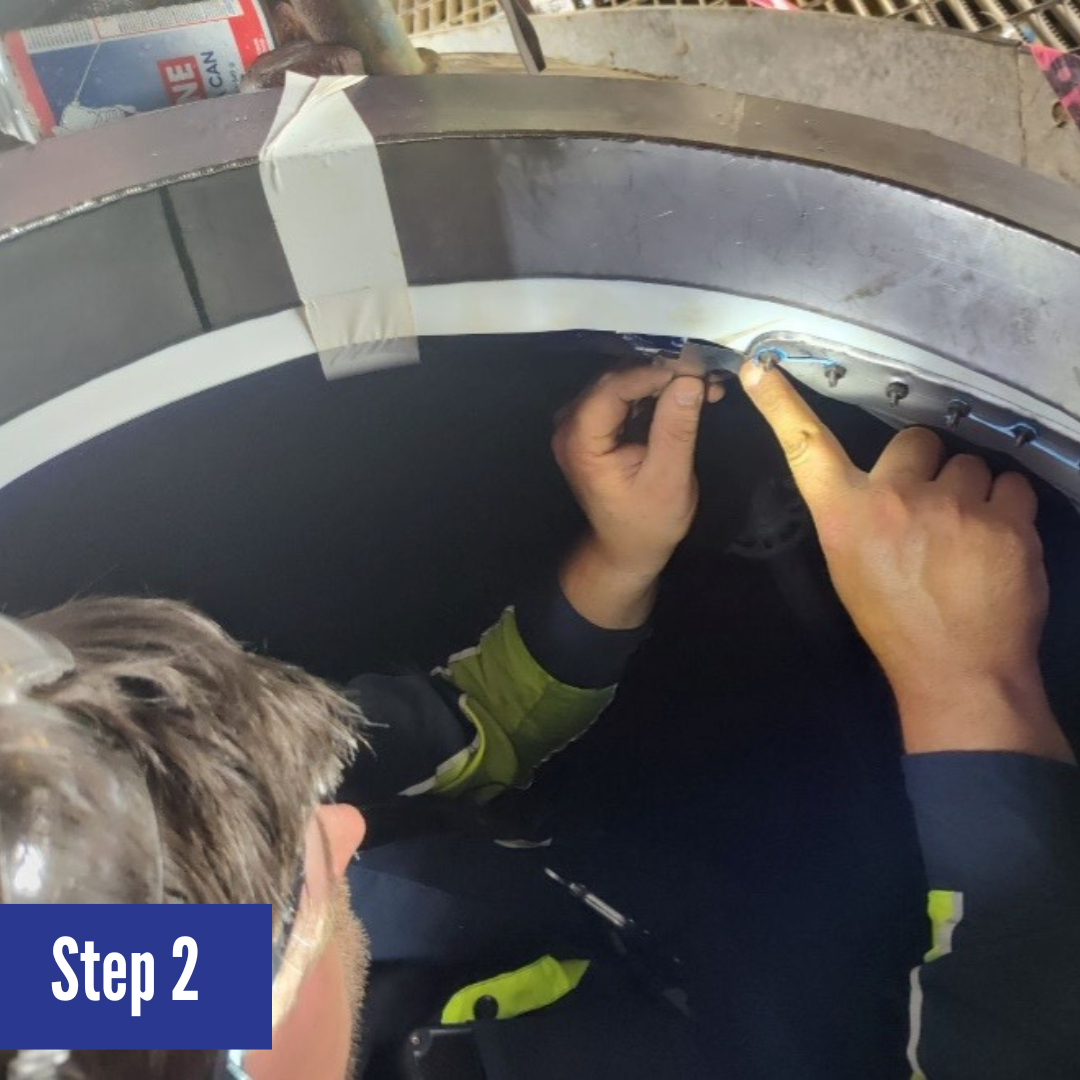
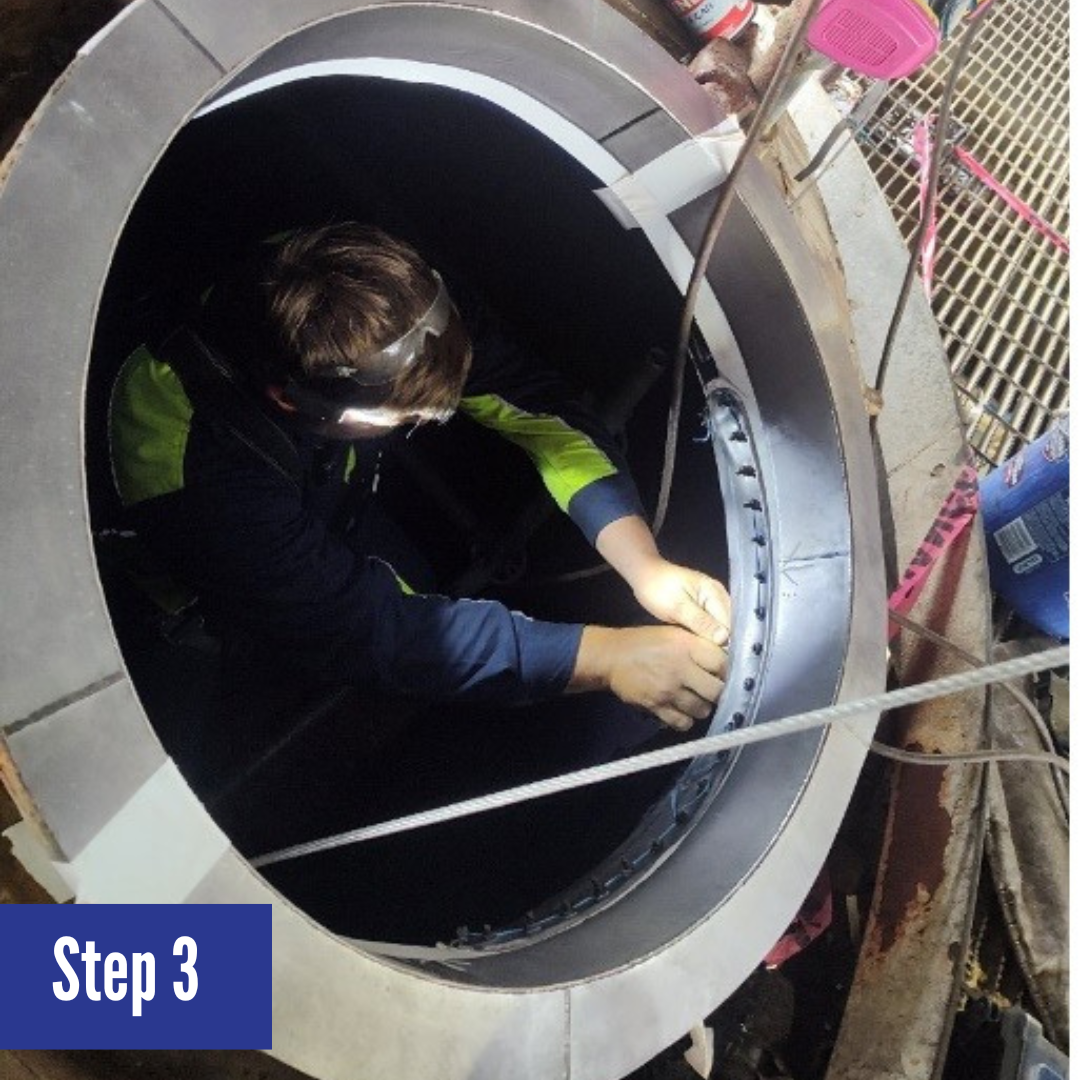


Attention to detail and precision are critical in reactor maintenance. Recently, Reactor 143 underwent a complex repair to address significant damage discovered during an inspection. Here's a detailed look at the process and what was involved in restoring the reactor to optimal working condition.
Initial Findings
Upon inspection, a hole was discovered below Reactor 143's 24-inch manway flange. This was a critical concern, as the vessel's integrity was compromised with a hole through the vessel shell. Glass damage extended from the manway flange along the manway neck past the swage radius then finally onto the top head of the reactor. Further inspection inside the vessel revealed extensive glass damage, indicating the need for immediate attention and repair.
Addressing the Damage
Preparing:
Clean and prepare the vessel for confined spaces entry.
Welding the Damaged Area:
The first step was to weld the damaged area carefully. This process was done very slowly to prevent further damage to the surrounding glass. Welding in this confined space requires safety along with a plan to prevent additional damage through thermal shock, ensuring the vessel's structural integrity was restored without causing additional damage.
Fabricating and Installing the Sleeve:
Fiberglass molds are created to replicate the radii and contours of the glass surface. A 24-inch tantalum outside sleeve is fabricated to meet the complex radii in the manway. Given the complexity of the repair, the patch required a custom mold to form it to several radii. This process involved extensive forming to ensure the patch fit perfectly, effectively sealing the area within .002”.
Replacement of Key Components:
The pro-ring, manway cover, and CRT Gaskets were replaced as part of the repair. To verify the integrity of the repair, the sealing edge was checked using .002" shim stock, ensuring that the patch was sealed.
Final Touches:
The installed patch was injected with furan, a filler material known for its chemical resistance and durability. The new manway cover and pro-ring were installed with fresh bolts and gaskets, securing the entire assembly.
Best Practices for Prolonging the Life of Reactor Components
To extend the life of the new sleeve and maintain the reactor's performance, it's recommended to:
Use CRT gaskets with tabs, The tabs will hold the gasket in position.
Replace the manway gaskets as soon as they show signs of wear.
Ensure torque clamps are tightened to 55 ft/lbs to maintain a secure and leak-free connection.
Reactor 143's repair was a complex and detailed process, but with careful planning and execution, the reactor was returned to production. By following best practices and performing regular maintenance, the lifespan of the reactor's components can be significantly extended, ensuring continued efficiency and safety in its operations. GTI is available to perform routine inspections, repairs, and root cause failure analysis.